L’elettroerosione (in inglese Electrical Discharge Machining) è una tecnologia di lavorazione non convenzionale inventata nel 1943 per la rimozione di materiale che si applica ai materiali buoni conduttori quali metalli, leghe metalliche, grafite e ceramici.
Gli utilizzi dell’EDM
L’EDM è un tecnologia molto potente all’interno dell’industria manifatturiera odierna ed è usata soprattutto per la realizzazione di stampi perché permette di ottenere un’elevata precisione.
La rimozione di materiale avviene tramite un processo termico grazie a delle scariche elettriche che si instaurano tra materiale in lavorazione ed utensile. Entrambi sono collegati ai poli di un generatore e devono essere immersi in un fluido dielettrico che solitamente è olio minerale o acqua demineralizzata.
Oltre che a consentire il passaggio della scarica elettrica, il fluido dielettrico serve anche a raffreddare l’elettrodo e a rimuovere il materiale dal pezzo in lavorazione.
La scarica elettrica produce una energia termica tale per cui localmente si raggiungono delle temperature di 8000-12000 °C e si ha la formazione di un canale di plasma. Il canale di plasma porta a fusione la superficie del materiale che vaporizza e si disperde nel dielettrico sotto forma di polvere.
L’utensile avanza sul materiale in lavorazione attraverso un percorso che porterà alla formazione della geometria voluta. Con questa tecnologia si possono ottenere le più complesse geometrie bidimensionali e tridimensionali, a patto che sia possibile il moto inverso dell’utensile per allontanarlo dal pezzo.
I parametri elettrici da impostare sono l’intensità di corrente (1-500 A), il voltaggio (centinaia di V), la frequenza di scarica (1-30 µs), la durata della scarica (1 µs – 2 ms), la polarità (diretta o inversa). All’aumentare dell’intensità di corrente e della durata della scarica, aumenta la quantità di materiale rimosso.
Due sono i fattori critici del processo: il tasso di rimozione di materiale (material removal rate, MRR) e il rapporto d’usura dell’elettrodo (electrode wear ratio, EWR) inteso come il rapporto fra il volume perso dall’utensile e quello perso dal materiale. E ovviamente si vuole che ci sia l’MMR più elevato possibile congiuntamente all’EWR più basso possibile.
Ci sono due tipi diversi di elettroerosione: a tuffo (EDM) e a filo (WEDM).
Elettroerosione a tuffo
Nell’elettroerosione a tuffo un elettrodo con opportuna geometria viene avvicinato al materiale in lavorazione; quando si giunge alla giusta distanza (gap) si innescano le scariche elettriche e viene rimossa una parte di materiale che corrisponde al negativo della forma dell’elettrodo.
In questo tipo di elettroerosione si usa la polarità diretta per cui il pezzo in lavorazione funziona da catodo, mentre l’utensile funziona da anodo; la durata dell’impulso è maggiore di 30 µs. Un servomeccanismo controlla che il gap tra materiale ed elettrodo rimanga costante durante la lavorazione. Il fluido dielettrico usato è un olio minerale.
Per un funzionamento ideale, l’utensile non deve subire eccessiva erosione e per questo deve avere elevata conducibilità elettrica ed elevato punto di fusione. I materiali più usato per gli utensili sono la grafite o il rame.
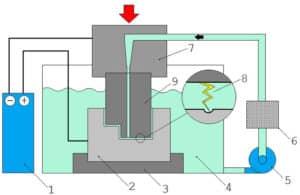
Schema dell’elettroerosione (EDM) 1. Generatore di scariche (DC) 2. Pezzo(+) 3. Portapezzo 4. Fluido dielettrico 5. Pompa 6. Filtro 7. Portautensile(-) 8. Scarica 9. Utensile
Elettroerosione a filo
In questo tipo di lavorazione l’elettrodo utensile è sostituito da un filo metallico di circa 0,2 mm di diametro e si usa la polarità inversa per cui il filo funge da catodo mentre il pezzo in lavorazione funge da anodo.
La durata dell’impulso è di circa 2 µs. Una macchina a controllo numerico comanda lo spostamento del filo. Il fluido dielettrico usato è acqua demineralizzata.
Solitamente sono lavorati con questo tipo di tecnologia le matrici di estrusione e i punzoni di taglio.
Conclusioni
I vantaggi di questo tipo di lavorazione sono l’assenza di forze di taglio, l’assenza di bave, la possibilità di realizzare geometrie complesse. Uno svantaggio invece è una velocità di rimozione materiale inferiore rispetto alle lavorazioni per asportazione di truciolo.
Il fatto che la lavorazione non dipenda dalle caratteristiche meccaniche del materiale come la durezza o il carico di rottura, ma solo dalle sue caratteristiche fisico-termiche, permette la possibilità di lavorare materiali molto duri che difficilmente si lavorano con l’asportazione di truciolo.
Le superfici lavorate presentano sempre un certo grado di rugosità a causa della creazione di micro-crateri, risultato dell’azione delle scariche elettriche.